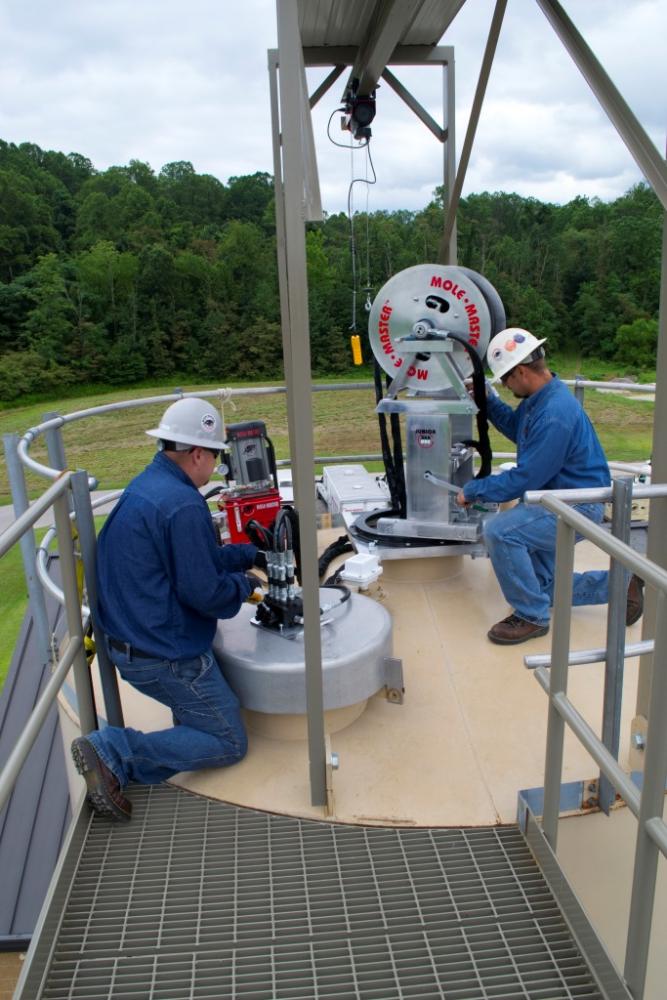
One of the biggest issues with storage silos is that many of the biggest problems that can occur can hide until it’s too late. Silo collapses or engulfment are not just extremely expensive for companies to recover from, but they can also be tragic. Far too many lives have been lost in recent years because of silo collapses or improper confined space entry. Companies are often left wondering how this could have happened. Indeed, an article in the June 2015 issue of Powder & Bulk Solids titled “Forensics Would Reveal Why Silo Collapsed” discussed how forensic engineering is needed in these cases to uncover exactly what caused the issue.
Silo collapses and engulfments are not the only issues your storage vessels may suffer. There are also countless preventable tragedies that occur in the process of trying to clear blockages or otherwise clean and maintain silos and other storage vessels.
How can a culture of safety extend to preventing these kinds of often-overlooked problems? How do problems like silo collapses occur in the first place? First, let’s offer some background into why silo collapses are becoming such a serious and common problem.
An Aging Infrastructure
Many of the silos standing today were built five or six decades ago. The assumption was that these silos were built to last and that they would be impervious to the effects of weather and time. Sadly, neither is proving true. The silos are getting worn from decades of being exposed to the elements. That is not the only problem, however. Over time, engineers have learned more about precautions that should be taken when building a storage vessel along with how material behaves inside silos. Engineers now know that in many cases, silos built in the 1940s and 1950s were not built the way silos are now. This will likely be the case again decades from today.
It’s Just a Crack
Unfortunately, denial is another huge contributor to silo collapse incidents. While not all warning signs are easy to spot, some certainly are, including cracks, bulging walls, protruding beams, or material leaking from one vessel to another. It is hard to overlook issues like that, but some companies are so worried about interrupting production that they will let these problems persist without calling a professional.
Moreover, many companies over the years have put off preventative maintenance and silo inspections for fear that serious issues would be found and production time would have to be stopped anyway. A shift to a safety first culture alters how these issues are perceived.
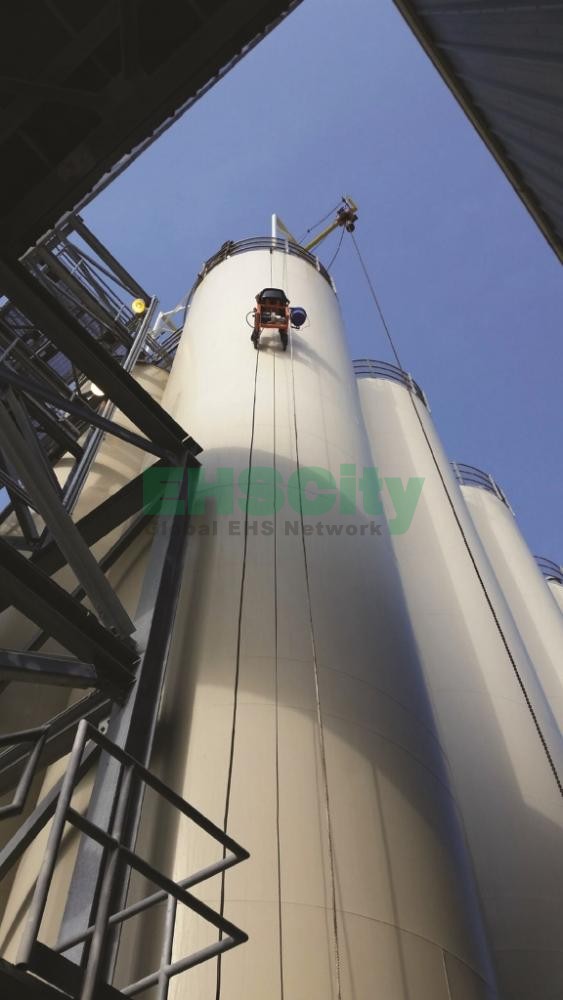
Failing to invest in silo inspections and in the safety of your workers around a storage vessel can easily lead to other problems. An employee sent to check on the roof of a silo could be endangered if the silo structure is not solid. Indeed, an employee tragically died because the roof supports of the silo on which he was working failed. There are countless incidents every year where workers are seriously injured or killed while trying to clean out a silo as well. Failing to observe all safety precautions can result in material collapse and entrapment. Again, a culture shift where safety becomes job one impacts all of these problems and processes.
Making the Safety Shift
once your company decides to emphasize safety, how can you approach these storage vessel issues more proactively?
Perhaps the most important step to take is to commit to regular silo inspections. These inspections will not only uncover structural issues, but they will also uncover any material build-up issues that could slow down or stop production.
Silo Inspections
Hiring a silo cleaning contractor and a silo engineer is the best approach for a silo inspection because the processes of silo inspections and silo cleaning often overlap. The engineer may find that the silo or vessel is actually too clogged to inspect, or perhaps he or she has the feeling that there are some unstable areas that would not be safe to work around. If that’s the case, silo cleaning may be necessary before the inspection process can continue. The advantage of conducting a silo cleaning at this stage is that potential dangers have already been identified, which will help to make the silo cleaning process even safer. Usually the roof beams need to be cleaned of dust before they can be inspected properly.
All of this may seem straightforward, and a facility may be tempted to draft current employees to engage in inspection or cleaning work. However, hiring engineers and contractors outside of the company’s payroll is important. A professional engineer will not have a vested interest in passing over any problems that become visible. He or she will want to make sure the job is done right and will provide an honest, third-party evaluation, whether the owner likes the results or not. Additionally, an engineer will be able to tell where potential problems exist, not just where problems are already surfacing. This is significant because prevention ultimately saves money over time. Asking a construction contractor to do a silo inspection can work, but contractors do not always understand silo behavior, and it is in their best interest to find issues that they can fix. Similarly, a professional silo-cleaning contractor will be able to work with the engineer to identify the safest entry points, potential problem areas, and can help avoid on-site hazards.
A silo inspection usually begins with a visual evaluation of the silo’s exterior. The naked eye will be used first, followed by the use of binoculars to get a close-up look at any potential problem areas. Vertical cracks on the exterior are clear signals of serious problems and usually are signs that the walls of the silo are weakening.
Next, the interior of the silo needs to be inspected. This is a key point where communication between the owner, the engineer, and the cleaning contractor is essential. If the silo has already been cleaned out, access can occur from the bottom. If the silo has not been cleaned out, the engineer will enter from the top and all work will occur above the build-up area for safety. once inside, the inspector will hit the silo wall in various places with a hammer. If there is a dull sound and/or vibration, this can be a sign of delamination, meaning that the steel support beams are separating from the concrete wall structure, which can eventually lead to a collapse.
After the inspection is completed, the engineer will take all photos and samples back to a lab for evaluation. In some cases, engineers will drill through certain troublesome areas so that the interior of the structure can be seen more clearly. Sometimes this helps clarify exactly how severe the problem may be. Shortly thereafter, a report will be presented together with recommendations.
The worst-case scenario following a silo inspection is finding out that the storage vessel is simply not stable enough to continue to be used. It may need serious repairs, or it may need to be replaced entirely. This is what companies tend to dread the most, but while this is a frightening outcome, certainly, it can also mean that lives are being saved. Had work continued on that silo, the roof or the walls easily could have collapsed, causing unnecessary tragedies like the ones described above.
Silo Cleaning
A “safety first” approach to cleaning and maintaining storage vessels is also extremely important. OSHA and MSHA provide detailed guidelines for approaching these tasks safely. A multitude of factors need to be considered. There needs to be extremely clear communication between the cleaning contractor and all employees, which is where the lockout/tagout process can be of assistance. If workers need to enter the silo, there are Confined Space Entry guidelines to follow, including proper harnessing and air quality monitoring. Ideally, methodologies will be engaged that do not involve human entry at all, as that is the safest approach to silo and storage vessel cleaning.
Safety is the Midas Touch
The benefits of adapting your culture to a safety first mentality are numerous. Obviously, your employees will be able to work in a safer environment, which is good for everybody. Knowing that your company is committed to safety is also important to your customers. When a company experiences a silo collapse or a similar incident, customers are reluctant to continue doing business with a company dealing with this kind of bad publicity. On the other hand, customers can be proud to work with you if they know you take great care of your employees. There is no better public relations theme than happy employees and happy customers.
Safety covers every facet of your plant. Don’t forget to include your approach to your storage vessels in your evolving way of doing business.
